Corrosion Resistance in Reinforcement
Why Corrosion Control of Reinforcement bars (Rebars) is necessary?
Corrosion control of steel reinforcement is necessary to prevent damage and failure of concrete structures. Nearly 40% of failure of concrete structures is due to corrosion of embedded steel reinforcement
There can be many causes for corrosion of reinforcement, but mostly it is related to the quality of concrete, environment, and quality of construction practices. So, the first step in corrosion control of rebar is to provide good quality of concrete through good construction practices. The quality of concrete materials, mixing, placing and compaction techniques and good workmanship can help control the rebar corrosion.
There can be many causes for corrosion of reinforcement, but mostly it is related to the quality of concrete, environment, and quality of construction practices. So, the first step in corrosion control of rebar is to provide good quality of concrete through good construction practices. The quality of concrete materials, mixing, placing and compaction techniques and good workmanship can help control the rebar corrosion.

Fig: Types of Cracks in Concrete due to Corrosion of Rebar
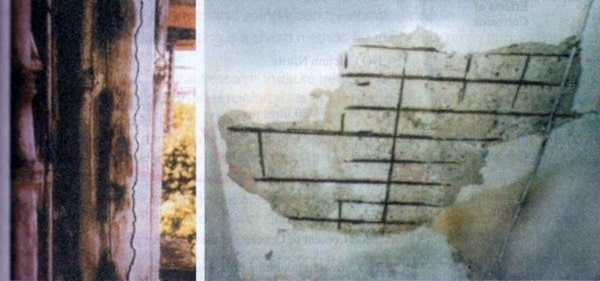
Though quality control in concrete construction may reduce chances of corrosion, there are various methods by which the corrosion control of reinforcement bars can be achieved.
Methods of Corrosion Control of Reinforcement in Concrete:
1. Cement-Polymer Composite Coated Rebars (CPCC)
Cement polymer coated rebars embedded in concrete are surrounded by an alkaline medium, thus cement based coating is more compatible for reinforcement corrosion control. Two coats of cement polymer are applied on rebar – Primer coat and Sealer coat.
Products involved in Cement Polymer Composite Coated rebar are:
- De-rusting Solution
- Alkaline Powder
- Phosphating Jelly
- Inhibitor Solution
- Sealing Solution
This system has been developed mainly as a factory / shop process.
Process of Cement Polymer Composite Coated rebar:
Sl. No.
|
Parameter
|
Requirements
|
1
| Surface preparation or pre-treatment | Sand blasting to the near white metal |
2
| Application of primer coat | To be applied within four hours of pre-treatment (sand blasting) |
3
| Application of sealer coat | Sealer coat to be applied within 30 minutes of primer coat application. Thickness of sealer coat should be 150+/- 25 microns |
4
| Air curing coated rebar | Cement polymer coated rebars should be air cured six hours before use in work. |
5
| Check for continuity of coating | No defects such as cracking, bulging, peeling, no rust marks. Visual inspection to be carried out. |
6
| Test for adhesion of coating | The coated rebars are bent at 120o around a mandrel. No peeling or cracking of coat should be observed on outer radius. |
7
| Stacking of coated rebars | Coated rebars to be stacked on buffer materials |
8
| Cutting, bending and welding of coated rebars | Coated rebars can be cut and bent. Cut ends and weld portion of the rebar should be treated with same formulation. |
The approach to development of this system is that the base metal of rebars contains pi electrons which get readily released in the corrosive environment leading to oxidation of iron and thereby formation of Ferrous Oxide (II) (rust) as a principal deterrent. In order to prevent this oxidation, a surface coating capable of interacting/nullifying the released electrons is provided.
Further prestressing and reinforcing steel, in concrete during service life, are exposed to an alkaline environment and this necessitates introductions of a top coat which should be compatible with primer and alkaline environment.
2. Fusion Bonded Epoxy Coated Rebars (FBEC)
Fusion bonded epoxy coated rebar is produced from 100% solid finely ground fused powder particles. These particles melt to form a continuous adherent film when heated. There is no passivating primer film provided in case of FBEC rebars. Fusion bonded epoxy coating introduces a medium of weakness in the path of an intimate bond between rebar and alkaline concrete.
Process of Fusion Bonded Epoxy Coated Rebars:
No. | Parameter | Requirement |
1. | Pre-treatment (Surface reparation) | 1. Bars are first cleaned from surface contamination such as oil, grease etc. by chemical process before shot blasting. 2. The reinforcement bars are cleaned by shot blasting or grit blasting to white or near white stage. 3. The blast cleaned bars are then heated through induction heaters at preset temperature level around 230°C. |
2. | Coating | Hot bars are then fed to the coating booth, where the epoxy powder is sprayed electrostatically. |
3. | Curing and Cooling | Coated bars are then cured and forced cooled by water spraying to enable handling and testing. |
4. | Continuity of coating | Online and offline holiday checks, thickness checks are carried out. The adhesion of the coated bars is also tested frequently by bending of the bar. |
5. | Testing of Performance of
rebar
| Various other tests are performed in laboratory like chemical resistance, short spray, resistance in continuance boiling water, abrasion resistance and impact resistance etc. These are conducted on every batch of production. |
6. | Handling & Stacking | Fusion Bonded Epoxy Coated Bars require padded contacts during transportation, stacking, handling and till the concreting is done. |
7. | Cutting, bending & welding | The cut ends, welded spots and handling damages are required to be repaired with special liquid epoxy compatible with the coating material as per specification of the coating agency. |

An extensive investigation carried out on 40 bridges in Florida Key in the USA has revealed that disbandment can occur easily in the FBEC rebars which lacked passivation layer of Ferrous oxide (II) and is a precursor to corrosion. Higher coefficient of Thermal Expansion of fusion bonded epoxies imposes large thermal stresses in epoxy coating leading to its early failure.
Table: Mandrel Diameter for Bend Test Requirements
Bar Diameter (mm) | Mandrel Diameter (mm) |
6 | 60 |
8 | 80 |
10 | 100 |
12 | 100 |
16 | 125 |
18 | 150 |
20 | 150 |
22 | 200 |
25 | 200 |
28 | 225 |
32 | 280 |
36 | 280 |
40 | 400 |
45 | 450 |
50 | 500 |
Epoxy coats the rebar in the following manner:
- Melts
- Flows
- Gels
- Cures
- Cools
- Adheres as coating
3. Corrosion Resistant Steel Deformed Rebars (CRSD)
Mechanism of resistance to corrosion begins with the formation of initial layer of protective oxide or rust. (Hypo oxides). Unlike common rust on normal rebars, the CRSD rust is passive, tenacious and self-renewing. The protective oxide is fine textured, tightly adherent and a barrier to moisture, oxygen, carbon dioxide, Sulphur dioxide and chloride effectively preventing further corrosion.
The scale on normal bars of steel is a coarse textured flaky oxide that does not prevent moisture or oxygen from reaching the underlying bars and continuing the corrosion. As corrosion resistance is in the chemistry of the grade, if the passive oxide layer gets removed somehow, a new passive layer is formed immediately.
Corrosion Resistant Steel Deformed Rebars – Mechanical Properties
Properties | IS:1786 Fe500D | CRSD |
Yield Stress, YS (min, N/mm2)
| 500 | 500 |
% Elongation
| 16 | 16 |
Ultimate Tensile Strength, UTS (min, N/mm2)
| 565 | 580 |
Comparison between Methods of Corrosion Control in Rebar:
Comparison between Cement Polymer Composite Coated rebar, Fusion Bonded Epoxy Coated Rebars, and Corrosion Resistant Steel Deformed Rebars:
Parameters
|
CPCC
|
FBEC
|
CRSD
|
Thickness of Coating | 175 mm – 300 mm | 300 mm – 675 mm | No coating required |
Type of Protection to rebar | Extrinsic | Extrinsic | Intrinsic |
Pre-treatment | Pretreatment is required before coating | Pretreatment is required before coating | No pre-treatment required |
Treatment to surface | Before coating the surface made little rough when some damage is introduced. | Before coating, the surface made little rough when some damage is introduced. | The surface of the finished good is not disturbed or damaged at all. |
Temperature treatment | The whole process is done at room temperature. | 230°C – 400°C | No treatment required |
Special Bending requirement | Modified mandrel diameter is specified by Indian Standard | Modified mandrel diameter is specified by Indian Standard | Same as other TMT rebars of Fe 500D grade |
Defects introduced | Holiday Effect | Holliday Effect | Nil |
Reference
- ‘Durability of Concrete Structures’, RDSO, India
- ‘Guidelines for the use of High-performance Concrete in Bridges’, RDSO, India
- IS: 13620 – Fusion Bonded Epoxy Coated Reinforcement Bars – Specification
- A775/A775M ? 07b (Reapproved 2014) – Standard Specification for Epoxy-Coated Steel Reinforcing Bars
- Corrosion Reinforced Steel in Concrete by Tonini-Guides – ASTM Special Publication 713
- Corrosion of Reinforcement in Concrete Construction by C.L. Pagci P.B. Bamforth, J.W. Figg (U.K.)
Comments